THE TM-1 MocK-up, MARCH 1964. The LM's
design was now greatly refined, It was still a twostage vehicle, with the
descent stage serving as the launch pad for the ascent stage. In 1964,
Grumman unveiled its wooden TM-1 mock-up to NASA. In order to save weight,
the LM now had four folding legs instead of five fixed ones. The LM still
lacked a ladder, as it was felt that if it bent upon landing, there would
be no way for the crew to descend; thus, a knotted rope was supplied instead,
Astronauts, however, found it impossible to climb up the knotted rope. |
|
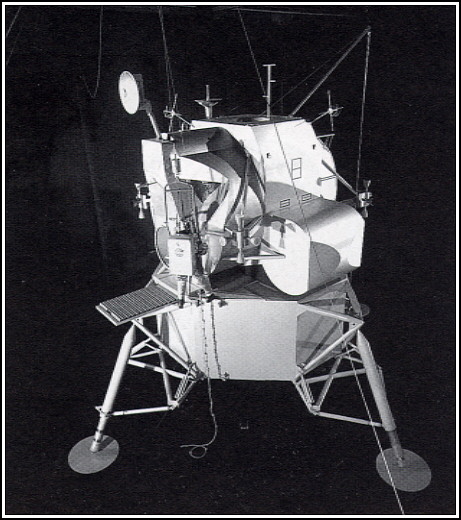 |